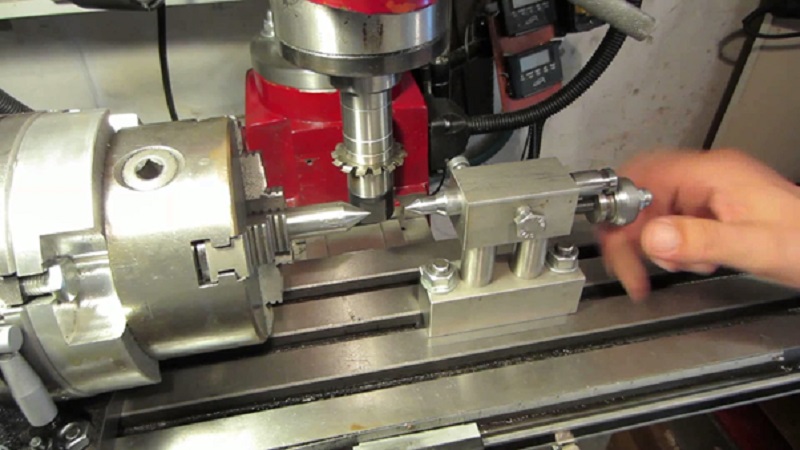
Metal Work on a Rotary Table: How It’s Done and Why It’s Good for Productivity
Rotary tables are very useful solutions that have found their way in dozens of different industries. Each industry has its unique demands, workflows, and production lines and this has led to a lot of different types of rotary systems based on the way they can move, such as vertical, horizontal, and hybrid machines.
On the other hand, given the type of work they are designed for, rotary tables can have air bearings, mechanical bearings, radial, or axial bearings, have drive motors, and so on. However, even with all their differences and specific designs, at their core, their functions remain the same.
The majority of rotary tables are used for machining metal work pieces and drilling. Let’s see how they are used for this kind of work and how they help increase productivity.
The setup:
Every new rotary table comes with a protective coating that needs to be removed before using the machine. In most cases, paint thinners can be used to remove the protective grease that is covering the surface of work areas.
Before the rotary table is used, it is important to adjust the indicator and turn the wheel to 0 degrees. The full degree indicator also needs to be aligned with an index line on the table.
Adjusting the worm.
To turn the table freely and set it up in a correct position, the user needs to disengage the worm. The assembly screw needs to be loosened, the vernier then needs to be rotated clockwise until the rotary table body indicator is aligned with the lone index line. After this is done, the worm assembly screw needs to be tightened.
To re-engage the worm, loosen the worm assembly lock, rotate vernier counterclockwise until vernier lines up with the rotary table body indicator. Tighten up the worm.
Locking the position of the table.
If the work that needs to be done on the rotary table is cutting, it’s essential that the table position is locked in properly so that the whole surface doesn’t start moving during operation.
The pressure of cutting could move the table and this will result in inaccurate cutting and maybe even cause injuries or damages to the machine. Make sure that the socket head is tightened properly within the locking clamps.
How to read dials?
The majority of rotary tables have three scales through which you control the position. The scale on the table has a total of one degree, the hand wheel scale has a total of two minutes, and the vernier scale located next to the hand wheel has a total of 10 seconds.
The first scale that needs to be looked at is the one that goes around the table. The minutes are read by locating the first line next to 0 indexes located on the vernier scale.
The seconds are identified by finding the lines on the vernier scale that matches the line on the hand wheel. If it is above 60, then count one minute and add the rest of the seconds.
How the rotary table is mounted:
A rotary table can be mounted in two ways:
- Horizontally
- Vertically
Based on your needs, you need to choose one or the other option. Set up the clamps properly and position the table, it is generally ideal to insert a small steel piece between the clamps and the table so that you can set it up more easily.
A rotary table is convenient and efficient.
After these essential preparations have been made, the chuck of your rotary table or some other similar part with the same function is attached. This part is designed to hold down objects that you will be working on.
When working on cylindrical objects which are longer, the work piece end also needs to be supported and you can use a tailstock to make it safer. A rotary table allows you to machine heavy metal work pieces in a precise way with great force and ensures that the quality of your work is top-level.
Both manual and automated machines can greatly benefit from rotary tables and allow you to work with precise cylindrical movement on various materials. There is less chance for making big errors, it allows you to work on more complex parts, and removes the need for changing setups regularly.
Remember that manual rotary tables are more suited for custom work that doesn’t require mass production and that CNC automated machines are better for mass production.