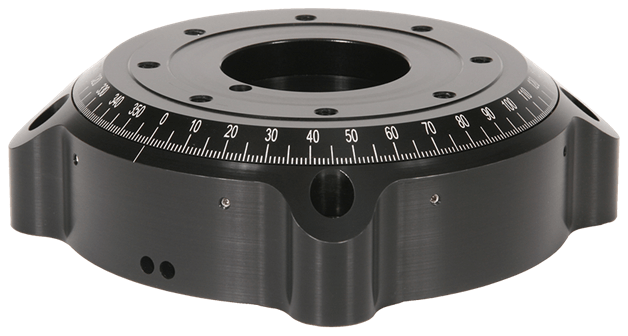
Rotary Stages for Rotary Motion
Rotary stages fall into the category of positioning devices that are used to achieve the highest precision possible in any rotary motion. These stages are composed of a rotating platform that is positioned on the top of a solid base and a rotary stage can be propelled by several different drive and technology options.
Each technology along with rotary stages have different features that are customizable and adjustable according to a specific need for load, eccentricity, wobble or velocity.
With an extremely wide range of standard rotary stages and other similar motion systems, every industry in the world can count on configuring the right motion solution for their unique and diverse needs and applications.
The reason why rotary stages or tables are so high in demand is that these stages address three main things that almost every industry needs: rotary parts of a motion system that includes yaw, pitch, and roll.
These three degrees of freedom of every part of a rotary stage is the main reason why these stages are so widely applied in production, manufacture, science, medicine, and so on.
Then, there’s the ability to vary things when it comes to the mounting orientation, which makes these rotary tables simply perfect, especially when it comes to those applications that demand the highest levels of precision in rotary positioning and motion.
Characteristics of rotary stages
Rotary stages have many different characteristics, as they are greatly utilized across a wide range of different fields of use.
Therefore, we will point out some of the most important characteristics to narrow down the field of use a bit, to show just how common these stages are in almost every industry in the world. The most essential, it’s even safe to say critical, characteristics are:
- Unlimited travel range
- Huge velocity range
- Third party and uniform software drivers
- Open loop
- Incremental encoders
- Absolute encoders
- Vacuum compatible
The first characteristic is perhaps the most important one, as many industries need high precision positioning devices such as rotary stages because of that unlimited travel range. It’s mostly because of that characteristic that these stages have such a wide field of use.
Applications such as automation, robotics, imaging or optical metrology, even sample positing need such high precision devices to give the most accurate results.
Therefore, it’s completely safe to say that rotary stages play a very important role in all types of rotary motion, as these stages provide the most accurate and precise results. If a rotary stage is used within Synchrotron, it’s a perfect set for beam lines, which can ensure precise results on a lot of important scientific research.
Aside from all this, these stages use a wide variety of actuator and bearing technologies and this makes them perfect in cases when very firm angular positioning at medium or low speeds is required. In such cases, it’s possible to mount special worm gears and precision lapped worms that are driven by a servo or stepper motor.
This can be extremely helpful in situations when there’s a static torque in the system due to the offset of the payload. Since it’s hard to obtain high levels of precision at high speed, rotary stages with direct drives are most recommended.
How to work with multiple stages
The most common use for rotary stages is as complete positioners with a single axis, but these can be easily integrated with additional rotary or linear axes. The most common use of such integrated stages is when a rotary stage is added to the top of an XY table.
This is where that travel range comes into play, as this is a very essential thing to consider. The total range of travel plays a critical role in situations and scenarios where a payload has been loaded onto the stage stack and needs to be precisely aligned. Since it’s a very limited travel range in question, this needs to be handled with delicacy and care.
Without the use of rotary stages, such an application couldn’t be possible because these are very small amounts of degrees we’re talking about here. Now, it’s also possible to mount two rotary stages onto each other, which allows for a multiple axes rotation.
So, more or less, working with multiple rotary tables makes almost anything possible, which is exactly why these tables are so valuable to numerous industries that require high levels of precision in positioning.
With the most recent advancements in modern technology, where precision plays a very important role such as the rotary motion industry, rotary stages are yet to play their most significant role.